FAMA BUYER’S GUIDE TC053 Mobile Breathing Air Systems
Mobile Breathing Air Systems
Prepared by the FAMA Body Subcommittee
This guide does not endorse any manufacturer or product
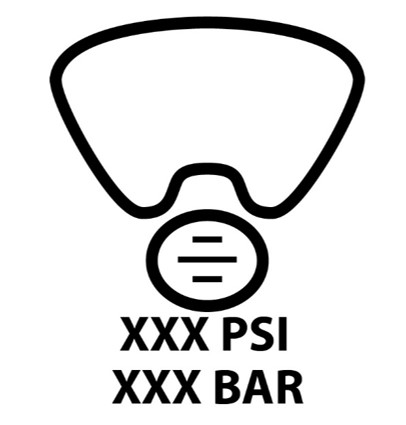
Contents
Introduction
This guide will provide fire service personnel with information about the various types of Mobile Breathing Air Systems that are available for fire apparatus.
As with any engineered system, there are pros and cons to each configuration and not all are listed herein. It is the responsibility of the procuring agency to determine what best meets their requirements and to convey this information to prospective fire apparatus manufacturer and/or sellers.
Technology is continually evolving. This guide is a general information and educational piece. The various options and auxiliary equipment presented herein may not be available from every manufacturer and some may be mutually inclusive.
The National Fire Protection Standards (NFPA) define voluntary minimum standards for automotive fire apparatus known as NFPA 1901. Chapter 24 of this Standard is devoted to Air Systems and is a comprehensive guide to the minimum specifications recommended for Mobile Breathing Air Systems including minimum component requirements, manufacturing guidelines and recommended installation requirements and certifications. This chapter should be the minimum to be required to be met in a set of bid documents and contract requirements. The purchasing agency and final agency inspector should become very familiar with this standard to insure a successful purchase and operation of the breathing air system. If a Mobile Breathing Air System is to be trailer mounted, then Chapter 26, Trailers, should also be included. The current editions should be referenced when specifying new apparatus. The can be found at www.nfpa.org.
Overview
This guide will present in general terms:
- Breathing Air System Components
- Drive Methods
- Breathing Air System locations
- Breathing Air System Selection
- Ancillary Equipment
Mobile Breathing Air System Components
Modern fire apparatus Breathing Air Systems are comprised of two or more major components to provide SCBA cylinder refilling on the fire scene and/or in station. The major components are the breathing air compressor, the SCBA cylinder fill station/enclosure, and the breathing air storage system.
BREATHING AIR SYSTEM COMPRESSOR
The breathing air system compressor is a specially designed high pressure multi-stage compressor to provide safe breathing air as defined in NFPA 1989. The compressor is rated by the horsepower (hp) requirement and cubic feet of air produced per minute (cfm). A general rule of thumb is that one (1) horsepower is required to produce one (1) cfm of air. Compressors for mobile applications generally are available in 10, 15, 20, 25, 30, 60 and 90 horsepower and produce 14, 20, 25, 30, 35, 60 and 95 cfm. The higher the cfm and horsepower, the greater the cost and the more air is produced. The compressor also provides the cfm required at a certain pressure per square inch (psi). The standard pressures available at this time are 5,000, 6,000 and 7,000 psi, however demand for 5,000 psi has fallen off significantly in recent years with the prevalence of 4.5 and 5.5 SCBAs. The compressor system also has the capability of cooling, moisture removal and filtering the air produced to meet the breathing air standards. This system is commonly referred to as the Air Purification System and consists of one or more mechanical filtration and chemical purification filters to accomplish this task. Another necessary component of the compressor is the electronic control system that monitors and controls the compressor’s functions, carbon monoxide (CO), dew point (dp), air discharge temperature and oil temperature.
SCBA CYLINDER FILL STATION
The next major component of the Breathing Air System is the SCBA cylinder fill station which also generally serves as the compressor control station. This is recommended as the operator of the fill station must be able to also control the compressor functions. The fill station is typically rated by the number of SCBA cylinders that can be simultaneously refilled. The most common are 1, 2, or 3-cylinder fill stations. The fill station will usually have an Air Control Panel to control the cylinder fill rate (which should not exceed 1,500 psi per minute (which is the highest rate recommended by the major SCBA cylinder manufacturers). It will also control the maximum psi that the SCBA is rated for. Current standards require that the fill station be completely enclosed and shall be independently tested to insure that the fill station shall contain a cylinder rupture inside the fill station enclosure.
There are two types of fill stations available. One manufacturer uses a design that permits the operator to fill two (2) SCBA cylinders in the chamber while attaching up two (2) additional empty SCBA cylinders on the outside of the chamber. The empty cylinders are then rotated into the fill chamber while simultaneously rotating the full SCBA cylinders outside the chamber. This permits a continuous fill cycle that significantly increases the fill rates per hour.
The second type of fill station is the most common where the SCBA cylinders must be connected and disconnected while no air is flowing. Most of these types fill stations have a flexible hose connection for each SCBA cylinder that must be screwed on to each SCBA cylinder to fill and screwed off by the operator before another group of empty cylinders can be filled. These fill stations are available for filling a single cylinder, two cylinders, or three cylinders, depending on the preference of the purchaser and the number of cylinder fills required per hour.
AIR STORAGE SYSTEM
The last major component of the Breathing Air System is the air storage system. The air storage system is composed of a group of transportable air tanks that have been certified to comply with 49 CFR 178.37. They are commonly known as ASME or UN/DOT air storage cylinders. They are typically combined into “banks” of 1 or more cylinders per bank and typically consist of 4 banks so that there is sufficient storage to meet the SCBA cylinder fill requirements needed for the agency.
The storage system can be plumbed for “bulk” fill or “cascade” fill, depending upon the user’s needs. “Bulk” fill is when you have multiple storage cylinders all plumbed together to the fill station air control panel so that they all fill or empty at the same rate. “Cascade” fill is when each storage cylinder is plumbed individually to the fill station air control panel so that each cylinder can be individually opened and closed to fill SCBA cylinders in a step process. The “cascade” method can be performed manually by the fill station operator or can be done automatically by an auto fill controller installed in or adjacent to the air control panel.
Drive Methods
The compressor is usually driven by an electric motor, diesel engine or hydraulically via power take off (PTO) from the vehicle transmission. There is also availability from apparatus manufacturers that provides dual power systems where the compressor can be driven by an electric motor or diesel engine. The electric motor in these types of units are usually powered by a shore power cord that is connected to a commercial power source located in the station or other facility that has rated power provision (typically three-phase). If the end user ops for this type of system, they must keep in mind that any electric motor with a rating of 10 horsepower or more requires 3-phase current at the power source.
If electric motor powered, the power is supplied by an on-board power take off (PTO) that drives a suitably sized generator. The end user must be mindful that they will need to specify approximately 2,000 watts of power for every compressor horsepower to insure they have enough capacity to handle the motor start up amperage.
Mobile Breathing Air System Locations
The breathing air system location must meet certain requirements in order to be a satisfactory installation to meet good practices to insure longevity and correct system operation.
The system is usually installed in one or more body compartments. The truck or trailer compressor compartment shall be of adequate size to accommodate the system and also provide suitable space to easily get to the components that need routine service. The compressor is air cooled and requires a constant supply of cooling air in order to insure that the filters reach their recommended change interval and quality air is produced. Remember that Carbon Monoxide is a product of combustion and high operating temperatures increase oil burning and carbon deposits within the compressor as well as hinder the moisture separation process. If space is limited or other restrictions exist, an exhaust fan that comes on automatically may be required. When installing in a mobile apparatus compartment the end user must be aware that no accommodations be made for storage of equipment on either side of the body in front of the compressor assembly. Doing so will restrict air flow and subsequent impact on proper operational conditions.
The compressor’s cooling fan is sized to move about 1,000 cfm of air per every 5 horsepower. Ambient temperature in the compressor compartment should not exceed 90° Fahrenheit when the compressor is running or additional cooling air is required. The ideal compressor compartment should be transverse with door openings on each side and absolutely no air flow restrictions that could block the cooling air path from either or both door openings. The compressor should always be wired to insure that both compartment doors are open before compressor will operate. Furthermore, the purification filters should be installed in the cooling air compressor air stream before the cooling air passes through the compressor. This will insure longer filter life.
The breathing air system SCBA fill station shall be located so that the fill station operator can easily reach all fill station controls. The loading height of the SCBA cylinder chambers shall be at a comfortable ergonomic height usually about waist high. Check the manufacturer’s installation guide for the fill station that has been selected to determine minimum height requirements.
Compressed air is extremely dangerous if a SCBA cylinder ruptures. There is enough force to physically damage the body structure of the apparatus as well as seriously injure the fill station operator if the sudden buildup of pressure inside the fill chamber is not instantly vented to atmosphere. Most fill stations require a clear opening of sufficient size to vent the force away from the operator with either an opening cut into the floor or rear wall of the compartment housing the fill station. The end user should work with the apparatus manufacturer during the fire apparatus design phase to make sure that the venting will not damage critical chassis components. The end user should be aware that if any filter or rubber insert is installed over these opening it may seriously impede the air blast flow. The third party testing of the system conducted for breathing air system manufacturer does not test the rupture containment with any form of obstruction in the blow out area of the chamber. Installing restrictive devices over the opening, especially once exposed to road spray, exposed the fill station operator to serious injury!
Note that weight distribution on the truck or trailer also is a very important consideration.
The air storage system shall be located where it is easily accessible for service. Relief valves and drain valves on ASME storage cylinders must be immediately accessible and drains should be plumbed to drain through compartment floor, making sure that no chassis components are directly under discharge points. End user must insure that when UN/DOT storage cylinders are incorporated as part of the system that they must be removed from the truck or trailer compartment every ten (10) years for required hydrostatic testing and they must be visible for inspection with expiration date clearly visible. Manufacturers/suppliers will not provide conventional DOT cylinders requiring inspection every five years. Expect manufacturer/supplier to not accept customer supplied storage cylinders for installation that do not comply with published standards or are within one year of requirement for hydrostatic testing.
Mobile Breathing Air System Selection
When procuring a mobile breathing air system for the first time or adding an additional mobile apparatus to the fleet, the end user will need to do an analysis of their needs for breathing air taking into consideration the following minimum factors:
- How many SCBA Air Packs do you have and do you have a spare SCBA cylinder for each air pack?
- On a typical call where you have depleted air packs, how many SCBA cylinders do you need to refill and is that number less than the spare SCBA cylinders that are on hand?
- Is there currently a stationary breathing air system or cascade system readily available that has the capacity to re-fill depleted cylinders and is it capable of re-filling current air pack cylinder pressure ranges?
- What is the pressure rating of current air packs? What is the capacity of each SCBA cylinder (30/45/60 minute bottles)?
- Do you have access to Mobile Breathing Air System(s) through a Mutual Aid Agreement? Has it worked well in past responses?
- In your response area, how many buildings or hazards do you have which would be great enough to require at least one or more SCBA cylinder replacements or refills on the scene should a working situation occur?
- Do you have cascade storage systems in various locations (mobile or stationary) that will require storage cylinder (vessels) to be refilled?
- Are they any aerial platforms with plumbed breathing air that will be required to be re-filled and how many?
Mobile Breathing Air System Selection (continued)
Once you have gathered all of this information, you should be able to determine if you need a mobile breathing air system. Many times in smaller departments, a cascade storage system with fill station is all that will be required, if the cascade system has immediate access to an air compressor refill system. Below are some facts about cascade systems that may be helpful;
A “cascade” plumbed four (4) cylinder UN/DOT storage system rated at 6,000 psi can fill one of the following groups;
48) 2216 psi 45 cubic feet SCBA cylinders; or
32) 4500 psi 45 cubic feet SCBA cylinders; or
16) 4500 psi 88 cubic feet cylinders; or
13) 5500 psi 45 cubic feet cylinders; or
7) 5500 psi 87 cubic feet cylinders
If, for example, your typical fire scene usage is twenty (20) 4500 psi 45 cubic feet cylinders, then a fill station and cascade system would meet your needs as you have a capability of filling 32 cylinders per the listing above. Then all you have to decide is whether to put one in the fire station or mount it on a truck or trailer. You must however figure out how to replenish the cascade storage.
If the mobile cascade system does not fulfill your needs, then a compressor system needs to be considered. The number of SCBA cylinders that can be filled per hour depends upon 3 factors;
- The compressor horsepower and cfm produced.
- The time it takes the fill station operator to perform one complete fill cycle of loading and connecting the cylinder(s), filling the cylinder(s) and disconnecting and unloading the cylinder(s).
- The number of cylinders that can be filled at the same time in the fill station.
Use the following tables to determine the approximate number of SCBA cylinders per hour that can be filled by a certain size compressor. This will serve as a guide but will not be 100 percent accurate as there are too many variables that the calculations do not take into account. These can include, but not limited too, things such as: (1) the skill of the fill station operator; (2) the amount of residual pressure in each SCBA cylinder that will be re-filled; (3) the pressure status of the storage system when re-fill operations begin; (4) the time it takes the compressor to remove/purge moisture; (5) the quantities of different pressure rated cylinders; and (6) the cf of different cylinders that are in the pile of cylinders to be filled.
The quantity of cylinders that can be filled in an hour may be governed by the maximum fill rate of 1500 psi per minute or the capacity of the compressor and storage.
The tables show the most common mobile breathing air systems available from the various manufacturers.
The cycle time is based upon using the most efficient fill station. If your selected fill station cycle times are greater than those in the table, your number of fills per hour will be reduced.
The maximum fill rate per SCBA cylinder manufacturers is 1500 psi per minute.
The tables are assuming that every cylinder is completely empty before it is refilled. A typical residual may be 500 psi or more, but it is not recommended that a residual be used in the calculations. The more residual (on average) that is available in the SCBA cylinders when staged for re-fill, the more cylinders that can be added to the total calculations.
Table 1 – 10 hp 14 cfm +/- 6,000 psi mobile air system, 4-bank manual cascade system
*after about 48 minutes, storage is depleted so compressor output is filling cylinders
** after about 25 minutes, storage is depleted so compressor output is filling cylinders

Table 2 – 20 hp 25 cfm +/- 6,000 psi mobile air system. 4-bank manual cascade storage system

Table 3 – DUAL 20 hp 25 cfm+/- 6,000 psi mobile air system Dual 4-bank cascades, dual 2-chamber fill stations. Auto sequencing cascade control

Table 4 – 60 hp 65 cfm 6,000 psi mobile air system, 10 ASME storage system, 3 2-chamber fill stations

Mobile Breathing Air System Selection (continued)
Once you have gathered all your information in the beginning of this section, pick the system above that best meets your needs. Then check with your selected mobile air system vendor to see what Ancillary Equipment options he has to make your selected system even better.
7,000 psi breathing air systems are now becoming available in stationary systems but, as of this printing, none are yet available for mobile applications. When mobile applications become available this data will be updated.
Ancillary Equipment
There are additional mobile breathing air products on the market that you may add to your mobile breathing air system to enhance your operations.
- High Pressure Air Reel plumbed to your mobile breathing air system will give you the ability to fill cascade systems, provide remote air supply for incidents requiring a breathing air supply etc. For safety purposes and to prevent serious injury, when using a reel in mobile applications a safety valve should be incorporated before the reel to that immediately shuts off air flow should the remote hose be damaged.
- Low Pressure Air Reel plumbed to your mobile breathing air system to provide utility air for pumping up tires, running air tools and jacks etc.
- Automatic Cascade System to take the operator error out of the cascade procedure.
- Automatic Cascade Management for multiple fill stations, storage and compressor.
- Air Control Panel 2 or 3 position selector to select the SCBA cylinder fill pressures quickly without having to turn a regulator control.
RFID sensor technology to record and store records of each SCBA cylinder filled including verifying correct fill pressure selected, who filled the cylinder, prevent filling a cylinder out of hydro, controlling fill station access, and cloud storage capability. Note that you would need to have this system installed on every one of your fill stations in order to have a complete record to meet NFPA record keeping requirements.
Manufacturer Contacts
For further information on apparatus and component manufacturers, refer to the FAMA Buyer’s Guide. https://www.fama.org/members/buyers_guide/