FAMA BUYER’S GUIDE TC033 AUXILIARY BRAKING SYSTEMS
AUXILIARY BRAKING SYSTEMS
Prepared by the FAMA Chassis Subcommittee
This guide does not endorse any manufacturer or product
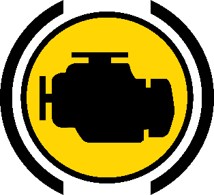
Contents
Introduction
NFPA 1901 Standard for Automotive Fire Apparatus requires that any apparatus over 33,000 lb GVW must be equipped with an auxiliary braking system. This means a system that assists in stopping the apparatus other than the service brakes located at the wheel ends. Auxiliary braking can be accomplished through the action of the engine, the transmission, or other means acting on the apparatus drivetrain. This guide describes the various types of auxiliary vehicle braking systems that are available on fire apparatus along with considerations that will help in selecting the right system for particular applications.
As with any engineered system design, there are advantages and disadvantages to each system. There are many commercially available products and not every system may be covered by this guide. This guide is presented as a general informative and educational piece, as technologies do continuously evolve. The various options and auxiliary equipment may not be available from every manufacturer, and you may not be able to specify more than one system on an apparatus.
Overview
Modern fire apparatus, like every other heavy on-road vehicle, are equipped with a braking system that uses friction to slow the vehicle. This friction comes from physical contact between a consumable material, and either metal drums or metal rotors. The contact force is created by either hydraulic force (typical in smaller vehicles) or by compressed air (typical in heavy vehicles). The air pressure in heavy vehicles is typically provided by a compressor driven by the engine.
The downside of friction braking systems is that they create heat that must be dissipated. The heavier the vehicle and the faster the stop, the more heat is created. In heavy braking situations this heat can cause the brakes to fade, or lose their braking power. This can occur if the brakes are used frequently, or consistently on long down-grades. In extreme braking situations the components can get hot enough to damage the brakes.
Auxiliary braking systems supplement the service brakes, increasing the stopping power and reducing the likelihood that the service brakes will overheat. The NFPA Apparatus Committee felt strongly that this capability was important in fire apparatus, which are more likely to brake hard and frequently. This is the reason that they began requiring auxiliary braking systems on large fire apparatus. In addition to these safety benefits, appropriate use of an auxiliary braking system will extend the life of the service brakes, reducing cost and frequency of maintenance.
Common Auxiliary Braking System Types
Commercially available auxiliary braking systems all use some method other than mechanical friction to help slow the vehicle. They also all work by creating a braking force on the vehicle driveline, which in turn transfers force to the tires and then to the road. They all generate heat, but they all control dissipation without heating up the service brakes. This guide covers the benefits of the following four most common types of auxiliary braking systems:
- Electromagnetic Retarders
- Exhaust Brakes
- Engine Compression Brakes
- Transmission Retarders
Electromagnetic Retarders
Electromagnetic retarders create their stopping power using the force that can be generated by a magnetic field. You can experience this force if you bring the north or south poles of two magnets together. In vehicle applications the magnetic fields are created by electricity flowing through a set of coils. The initial electric power to generate the field comes from the vehicle batteries, and is replaced by output from the engine alternator. Additional electric power is generated through the rotating action of the system
The electromagnetic retarder has two major components, the stator (stationary part) and the rotor (rotating part). When electromagnets in the stator are energized, this creates eddy currents in the rotor(s) as they rotate through the magnetic field of the stator. This results in forces that are acting to stop the rotor from rotating. Braking occurs when these forces create torque opposite to the rotation of the driveshaft. Heat is generated as a result of this electromagnetic interaction which is dissipated through cooling fins on the rotors.
Electromagnetic retarders are separate from the engine and transmission and must be mounted in the driveline. The two most common methods are:
Frame Mounted
- In this method the stator and rotor assembly are mounted inside the frame rails. The driveshafts are attached to the input and output of the retarder. This method has the advantage of providing a solid mount for the components, but may stretch the driveline requiring an increase in wheelbase. This method is referred to as an “Axial Mount” retarder.
Axle Mounted
- In this method the stator and rotor assembly is an integral part of the rear axle. In tandem axle applications the forward axle houses the retarder. This method takes less space in the driveline, but increases the mass of the moving axle, and exposes the retarder components to the axle motion. This method is referred to as an “Focal Mount” retarder.
Electromagnetic Retarders (Continued)
Electromagnetic Retarders provide maximum power at higher driveline speeds. As the vehicle speed drops so does the generated magnetic field. Retarders are generally sized on the basis of overall gross vehicle weight and universal joint capability. They can be sized to provide more retarding than the vehicle’s engine can produce.
Pros:
- Quiet operation
- Able to provide braking when the engine is not running or transmission in neutral
- No specific maintenance required
- Electromagnetic retarders provide faster reaction time than hydraulic retarders
- Progressive braking based on pedal position
- No wearing parts or fluid replacement required
- Can be integrated with ABS systems
Cons:
- Operator training needed on general use and when to use in slippery conditions
- Consumes vehicle electricity to operate – may require a larger alternator
Exhaust Brake
Every internal combustion engine takes in air through the air intake and gets rid of it through the tailpipe. If you were to stop up the tailpipe so that no exhaust can escape the engine would stop rotating. This is the affect that the exhaust brake uses to provide braking power. An exhaust brake is a device that creates restriction in the exhaust system. This restriction increases pressure in the exhaust manifold which in turn applies pressure on the piston during the exhaust stroke of the engine. This acts against the rotational inertia of the engine resulting in braking force being transmitted to the driveline and subsequently to the tires and the road.
Historically exhaust brakes were simple devices consisting of a guillotine or butterfly type valve downstream of the turbocharger. This valve is modulated to reduce the exit area of the exhaust gases creating higher pressures in the exhaust manifold.
In modern engines, this back pressure can be created by the variable geometry turbocharger (VGT). A shroud moves within the turbine housing reducing the exit area for exhaust gas. This restriction results in a higher exhaust manifold pressure. Braking force is highest at high engine rpms, decreasing as the engine speed slows.
Pros:
- Least expensive auxiliary brake.
- Engines with Variable Geometry Turbos are able to provide exhaust braking with no additional hardware.
- More quiet than engine compression brakes.
Cons:
- Provides roughly half the braking power of traditional engine compression brakes
- For non-VGT systems, may require periodic maintenance or adjustment of the valve.
- No multiple settings available – on/off operation
- Limited braking force at low engine rpms
Compression Brake
A compression brake system was first commercially available starting in 1961 from the Jacobs Manufacturing Company, commonly referred to as the “Jake Brake”. Just like the exhaust brake, the compression brake using the “pumping” action of an internal combustion engine to create braking power. But where the exhaust brake uses a device external to the engine block, the compression brake uses the valves of the engine itself. The exhaust valves normally open to allow gases out of the cylinder after the power stroke. The compression brake system keeps fuel from entering the cylinders and changes the way the valves open and close. When braking force is called for, the system allows the engine to compress the intake air, but then releases this air to the exhaust stream before it can push back. This type of brake converts the engine from a power producing device to a power absorbing device. In effect, the engine becomes an air compressor.
An engine compression brake uses a mechanism to open the exhaust valves near the end of the compression stroke of a diesel engine. Exhausting the compressed air from the cylinder takes energy away from the piston as it returns to bottom dead center. Some systems also open a companion cylinder’s exhaust valve during the intake stroke to allow more air into the companion cylinder’s compression stroke. Because there is more starting pressure, it takes more energy to compress the air in the companion cylinder.
The engine compression brake works only when the operator is not depressing the accelerator or clutch pedals. Like the exhaust brake, the amount of braking available is dependent upon engine speed (higher rpm results in greater braking force). The maximum braking force a particular engine can produce is dependent upon factors such as the compression ratio, and engine displacement. Some engines can create as much braking horsepower as they produce for forward motion.
A compression brake system was first commercially available starting in 1961 from the Jacobs Manufacturing Company, commonly referred to as the “Jake Brake”. Today the mechanics required to create compression braking are inherent to most heavy duty diesel engines and are available as a factory OEM option.
Pros:
- Less expensive than other retarder systems
- More braking force than traditional exhaust brakes
- Minimal maintenance required – adjust when setting valves and injectors
- User selectable braking level
- Can integrate with cruise control for automated application
- Controls integrated with automatic transmissions which enables downshifting for greater braking
- Smooth operation
Cons:
- Can result in additional exhaust noise not allowed by some city ordinances
- Operator training needed on general use and when to use in slippery conditions
- Limited braking force at low engine rpms
Transmission Retarder
Where the service brakes use mechanical friction to stop a vehicle, the transmission retarder uses fluid friction. Inside the retarder housing there is a vaned flywheel that rotates at the speed of the transmission output shaft. In normal operation, this flywheel is spinning in a cavity with air around it. This spinning creates minimal drag on the driveline. When auxiliary braking is called for the cavity is filled with transmission fluid. This fluid is churned by the vanes in the flywheel creating drag. The more fluid in the cavity, the greater the braking force.
This churning action slows the vehicle, but it also heats up the transmission fluid. Chassis designers must take this extra heat in to account when designing the cooling system. The transmission cooler capacity is increased and the rest of the system is designed to accommodate the heat.
Pros:
- Work independent of engine speed or transmission gear ratio
- Powerful retarding force even at low vehicle speeds
- Integrated within the transmission and controlled by the transmission controller
Cons:
- Generate heat that must be dissipated by vehicle cooling system
- More costly than exhaust brake or engine compression brake
Control Methods
While applying the service brakes is a straight-forward push on the brake pedal, auxiliary brake control offers many more possibilities. Not all possible control methods are available with all auxiliary brake types. Here are some of the potential methods, consult with your apparatus manufacturer to select a method that is available on the brake type you select:
- Full on when the accelerator pedal is released
- Full on when the brake pedal is depressed
- On when the brake pedal is depressed, with progressively increasing braking as the pedal is depressed farther.
- Separate hand lever
System Comparison
There are many considerations when selecting and auxiliary vehicle braking system. Each method has its own benefits, disadvantages, and costs. The good news is that apparatus manufacturers have been installing all of these systems for decades and the technology is mature. The following table presents a general comparison of each method:
* On engines built after 2002, variable geometry turbos can act as a low cost exhaust brake. External exhaust brakes are more expensive.
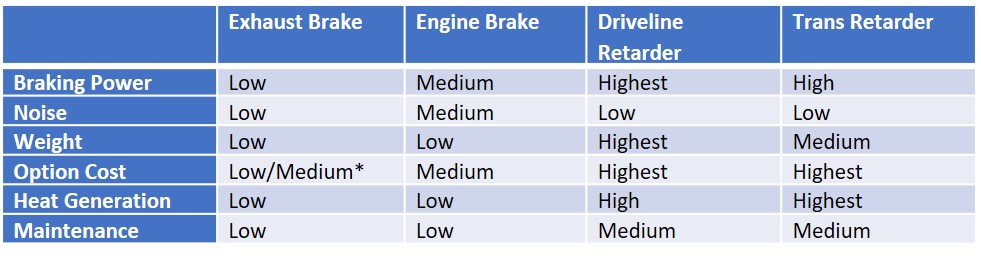
Additional Resources
For more information contact your apparatus manufacturer, or the FAMA engine, transmission or electromagnetic retarder supplier listed in the buyer’s guide at www.fama.org.