Batteries, Alternators, and Chargers
FAMA BUYER'S GUIDE TC035 Batteries, Alternators, and Chargers
Batteries, Alternators, and Chargers
Prepared by the FAMA Electrical Subcommittee
This guide does not endorse any manufacturer or product
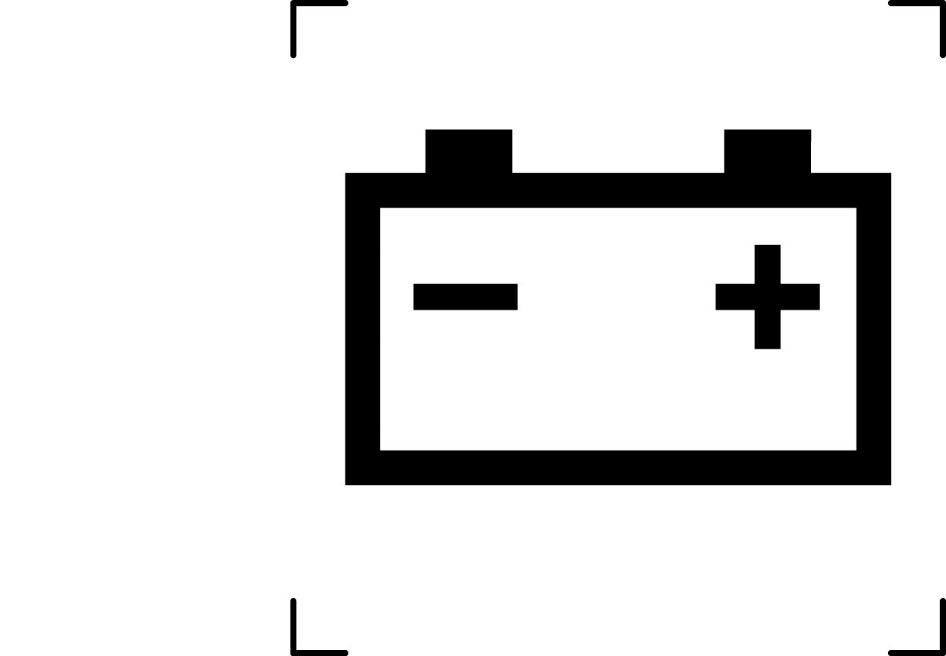
Contents
Introduction
The charging system is one of the most vital parts of any vehicle. The three main components of a Fire Apparatus charging system are the batteries, alternator, and charger. All three work in conjunction to keep the vehicle and its many systems operating correctly. When choosing a charging system all three components should be selected to insure that they will support each other properly.
Overview
When selecting batteries there are many different chemistries available to choose from. Each of these chemistries has different properties, as such what might work great for some may have issues in a different application. Each application and budget will have to look into what will work best for them.
In terms of the alternators there is a new push towards compensated charging. In the old days many alternators worked on a simple locked voltage output. Now many alternator manufactures are taking into account the dynamic nature of batteries. Many have come out with remote voltage and temperature sensing capabilities. These allow the alternator output voltage to fluctuate to better charge the batteries at their preferred rate. Also with the push to electrify more and more of an apparatus higher output alternators are necessary to keep up with these ever increasing demands.
With chargers there have been many different options that can be placed on an apparatus. One of the most important considerations when choosing a charger is the total parasitic draw an apparatus has. Historically many departments chose a charger based on the charge draw of the batteries alone. With higher key-off draws from radios, flashlights, and computers the need for a higher output charger has arisen. As a charger is only good when in use many manufactures have developed systems to assist crew and driver with plugging in and removing the plug without causing damage or harm.
Batteries
Batteries are typically made of six galvanic cells in a series circuit. Each cell provides 2.1 volts for a total of 12.6 volts at full charge. Each cell of a lead storage battery consists of alternate plates of lead (cathode) and lead coated with lead dioxide (anode) immersed in an electrolyte of sulfuric acid solution. As the battery discharges, the acid of the electrolyte reacts with the materials of the plates, changing their surface to lead sulfate. When the battery is recharged, the chemical reaction is reversed: the lead sulfate reforms into lead dioxide. With the plates restored to their original condition, the process may be repeated.
FLOODED LEAD ACID
Most starting lighting ignition (SLI) batteries are flooded lead acid. These are most recognizable as there is access to the cells to refill the water in the battery. Flooded Lead acid batteries are filled with an electrolyte (36% sulfuric acid, 64% water). During charging, gassing occurs, and water vapor escapes. Batteries must be periodically filled with water. Static charge voltage at room temperature Lead-antimony 2.35V/cell= 14.1V.
MAINTENANCE FREE/ LOW MAINTENANCE
Maintenance free batteries differ from flooded lead acid batteries in that the cells are now sealed. This is done through a change in the chemical makeup of the plates of the cells. Most commonly calcium, cadmium or strontium are use in place of antimony which produce less gassing and self-discharge. Static charge voltage at room temperature Lead-calcium 2.45V/cell= 14.7V.
ABSORBED GLASS MAT (AGM)
AGM batteries differ from flooded lead acid batteries in that the electrolyte is held in the glass mats, as opposed to freely flooding the plates. Very thin glass fibers are woven into a mat to increase surface area enough to hold sufficient electrolyte on the cells for their lifetime. The fibers that compose the fine glass mat do not absorb nor are they affected by the acidic electrolyte. These mats are wrung out 2–5% after being soaked in acids, prior to manufacture completion and sealing. The plates in an AGM battery may be any shape. Some are flat, others are bent or rolled. AGM batteries, both deep cycle and starting, are built in a rectangular case to BCI battery code specifications. Static charge voltage at room temperature Lead-tin 2.45-2.50V/cell= 14.7-15.0V.
CHARACTERISTICS
Reserve Capacity: Number of minute’s battery can produce 25 amps and maintain 10.5 volts.
Cold-Cranking Amps (CCA): Amount of current battery can produce at 0°F for 30 seconds without going below 7.2 volts.
Cranking Amps (CA): Amount of current battery can produce at 32°F for 30 seconds without going below 7.2 volts.
Specific Gravity: The weight of a given volume of liquid divided by the weight of an equal volume of water. Water has a specific gravity of 1.000. In a battery the closer to 1.000 the specific gravity the less acid content of the battery (discharged).
Alternators
Alternators are used once a vehicle has been started to recharge the electrical power of the batteries used to crank the engine. In addition, they provide the current to operate all of the electrical accessories while the engine is running. Current is produced in an alternator by the principle of electromagnetic induction. As a magnet is passed over a coil of wires it induces a current into those wires. This current is then sent through a diode rectifier to become the needed DC output.
COMPONENTS
Field coil: Coil of wires wrapped around an iron core. When current is passed though the coil a magnetic field is produced.
Rotors: Creates the rotating magnetic field of the Alternator. Can be solid metal or stacks of laminate metal attached to the shaft of alternator. With the field coil the shaft/rotors become the electro magnet.
Stators: Contains three main sets of windings wrapped around a laminated, circular iron frame. The coils of each winding are evenly spaced around the core. As the magnetized rotor passes by each coil voltage is induced into the coil creating an alternating current output. Stators can be wound in either Delta or Wye connection. In a Wye connection one lead from each winding is connected to one common junction. From this junction point the leads branch out in a Y pattern. In a delta connection the lead of one end of the winding is attached to the lead at the other end of the next winding. Delta connection are used where high amperage output is required.
Diode Rectifier: An assembly of power diodes that convert AC current output of alternator stator phases to DC current output. Rectifier assemblies are contained in the rectifier housing and can be stud-mounted diodes embedded in potting material that provides protection from damage and corrosion or diodes grouped in single blocks or modules.
TYPES AND OPTIONS
Brushed: Brushed alternators are ones where the power being delivered to the field coil is supplied to slip rings through brushes. These are the most common automotive design. Over time brushes and slip rings wear and require repair or replacement.
Brushless: Brushless alternators are where the field coil is held in place. There are no slip rings or brushes in a brushless alternator. The only wear items in a brushless alternator is the bearings. Brushless alternators are less susceptible to dust or dirt than brushed alternators.
Remote Voltage Sense: With Remote Sense, a second wire reads the actual voltage at the battery and signals the alternator to increase its voltage output to compensate for voltage drop, ensuring a constant 14 volts at the battery.
Temperature Compensated Charging: Battery based temperature voltage control features are able to automatically adjust charge voltage rate to ensure that batteries receive optimal voltage level for all types of batteries in all climates. The battery voltage sense allows the regulator to compensate for cable/connection voltage drop up to 1V. Remote temperature compensation reduces battery gassing and sulfating
Overvoltage Cutout: Special feature of some regulators that interrupts the field coil circuit, turning off the alternator if a prolonged overvoltage condition in the vehicle’s electrical system occurs. The OVCO circuit is often designed as a resettable circuit.
OUTPUT
Alternators are rated using a Society of Automotive Engineer’s standard (SAEJ56). There are some common points used in many specs to denote the power potential of an alternator.
Rated Output: This is the output at machine stabilized temperature (72F) alternator 6000 RPM. This is the most common number listed for an alternator’s output. A major issue with this number is that in many diesel applications alternator speed is 3:1 of the engine. So an alternator at 6000 rpm would require the engine to be at 2000 rpm.
Idle Output: A much more realistic and usable number is output at idle. This is most diesel engines idle from 700-1000 RPM so an alternators output at idle would be 2100-3000 RPM. This is a more relatable number as in many fire apparatus after the sprint to the call the vehicle will spend its most time idling at the call.
Chargers
Chargers are used to maintain the charge of a vehicle while the engine is off. In modern vehicles there are modules and computers that have a consistent parasitic draw on the batteries. These added with the many radios, flashlight chargers, and other loads can quickly deplete the vehicle batteries.
Input: Many chargers use standard wall outlet plugs to provide the needed power to charge the vehicle batteries. Another option in supplemental charging is solar panels. These panels provide a small trickle voltage that will assist the charger when the vehicle is outside.
Output: A major consideration in choosing a charger is the requirements of the vehicles parasitic draw. Many batteries require at least 5 amps to maintain charge. This is needed per battery and in addition to the parasitic draws on the vehicle. So if a vehicle has 6 batteries it requires at a minimum a 30 amp charger.
Mounting: In many cases a charger will be fitted onto the vehicle itself. There are several options for size and location of charger mounting. Some units are made waterproof to allow mounting in a water susceptible location. Other units are made with low profile in mind to allow mounting on small apparatus and vehicles.
Cable Ejecting: On some models the operator/driver must manually remove the cable from the vehicle. To help solve the issues of drivers leaving with the cable still plugged in, some manufactures have made auto-ejecting sockets. On these auto-ejecting units the wall plug cable is forced out once the ignition is switched on. This helps save time and prevents damage to vehicle, building electrical system, and personal.